Specials Case Studies
- Home
- Charcroft Manufacturing
- Specials Case Studies
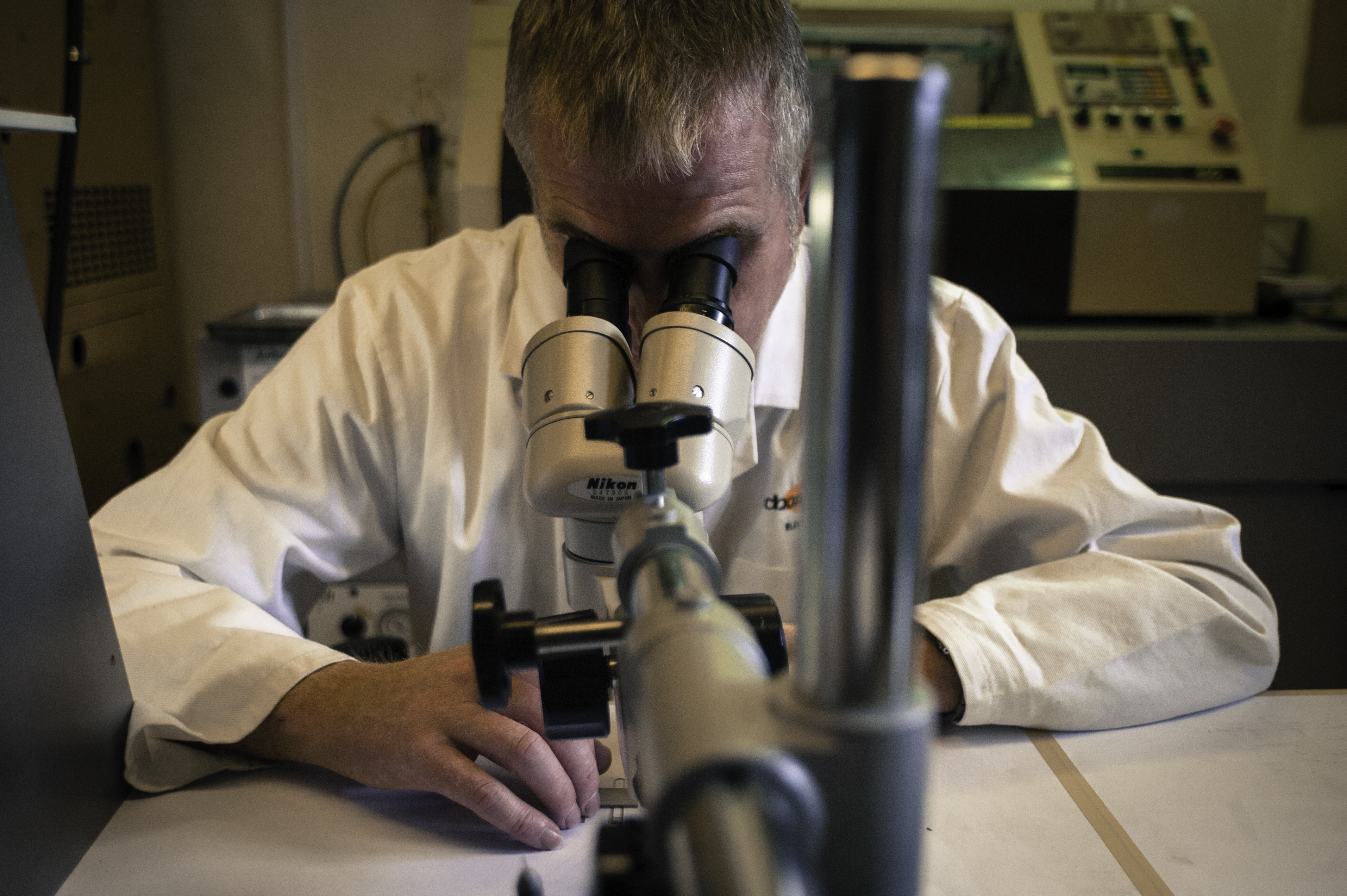
Charcroft Electronics are able to offer in-house manufacturing options for custom parts and projects in our BS- and CECC-approved UK production facility.
We can offer bespoke, custom assemblies to customers’ requirements, including flying leads options, custom labelling and printing. With no minimum order quantities, short lead-times, and in-house testing capabilities, we can provide a differentiated service package to our customers.
Charcroft Manufacturing can offer assistance with special projects, including the following requirements:
- Light manual assembly (nut and bolt)
- Hand soldering to J-STD-001
- Epoxy resin encapsulation
- Electrical harness manufacture
- Wire cutting and stripping
- Crimping and light riveting
- Heat shrink fitting
- Taping and reeling
- Component screening/binning, burn-in
- Third-harmonic, component linearity testing
We have been able to support a number of customers with solutions to their problems by offering specialist technical solutions, design support, low production volumes and prototype builds. Contact us to find out more about how we can help you, or you can read more about how we have helped our customers in our case studies below.
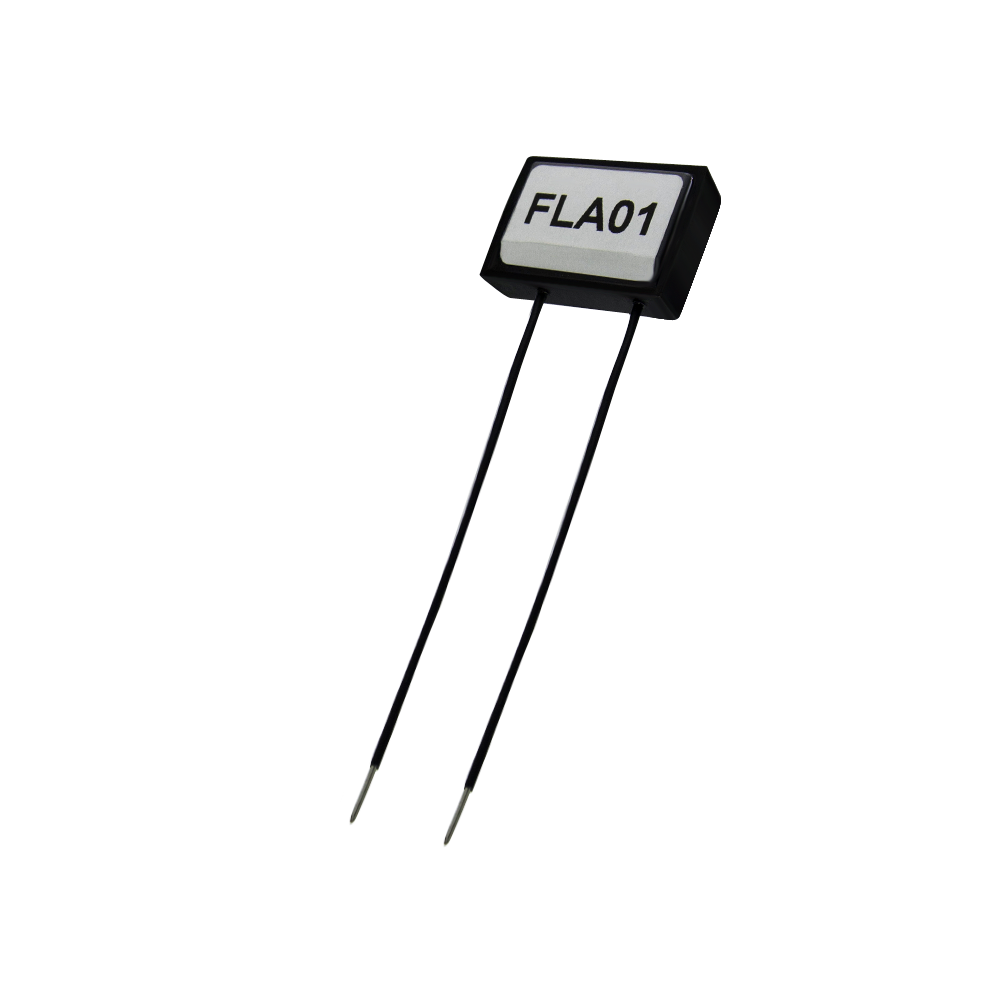
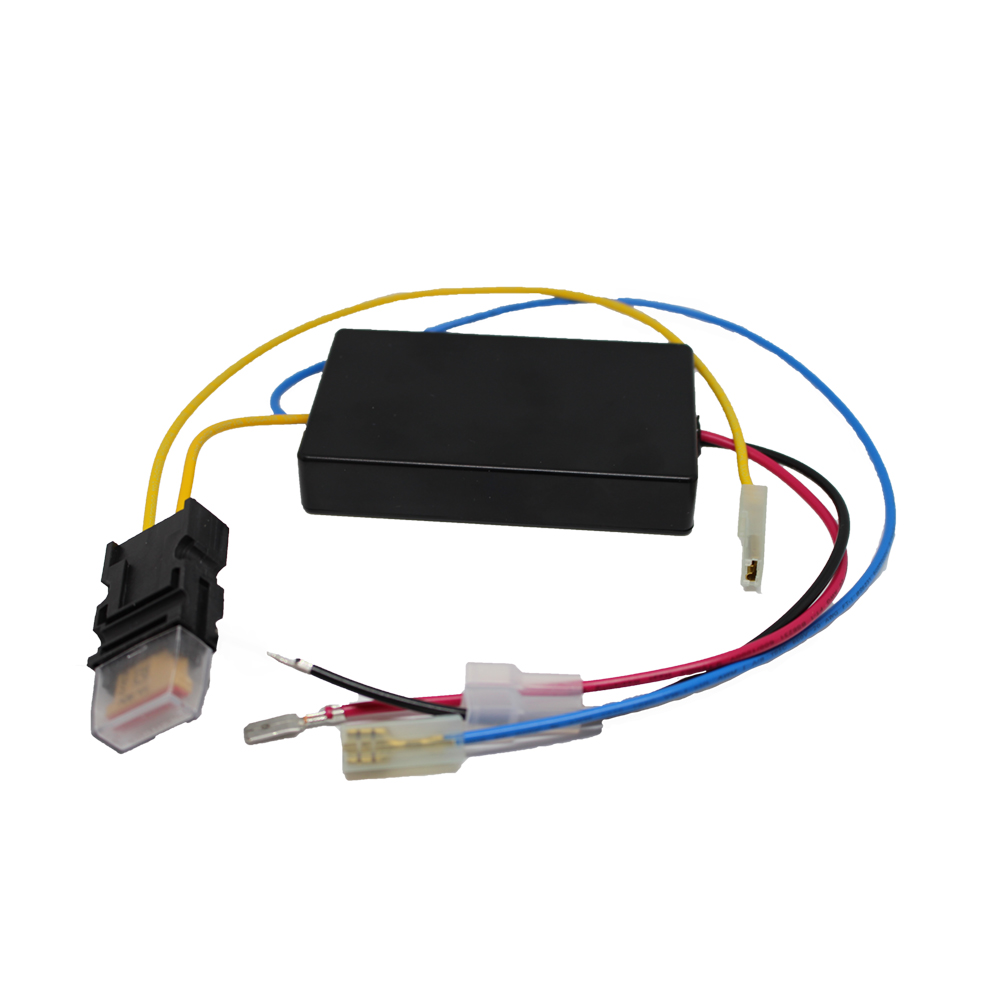
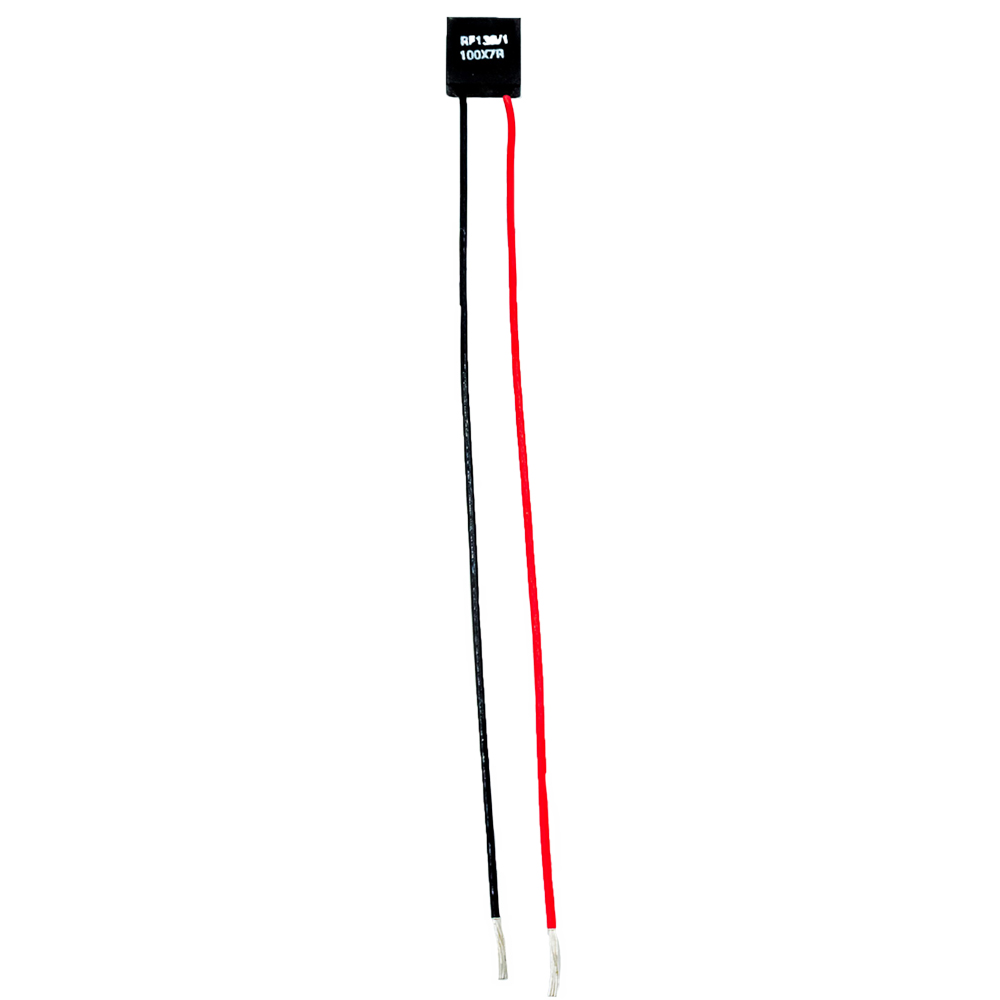
Case Studies
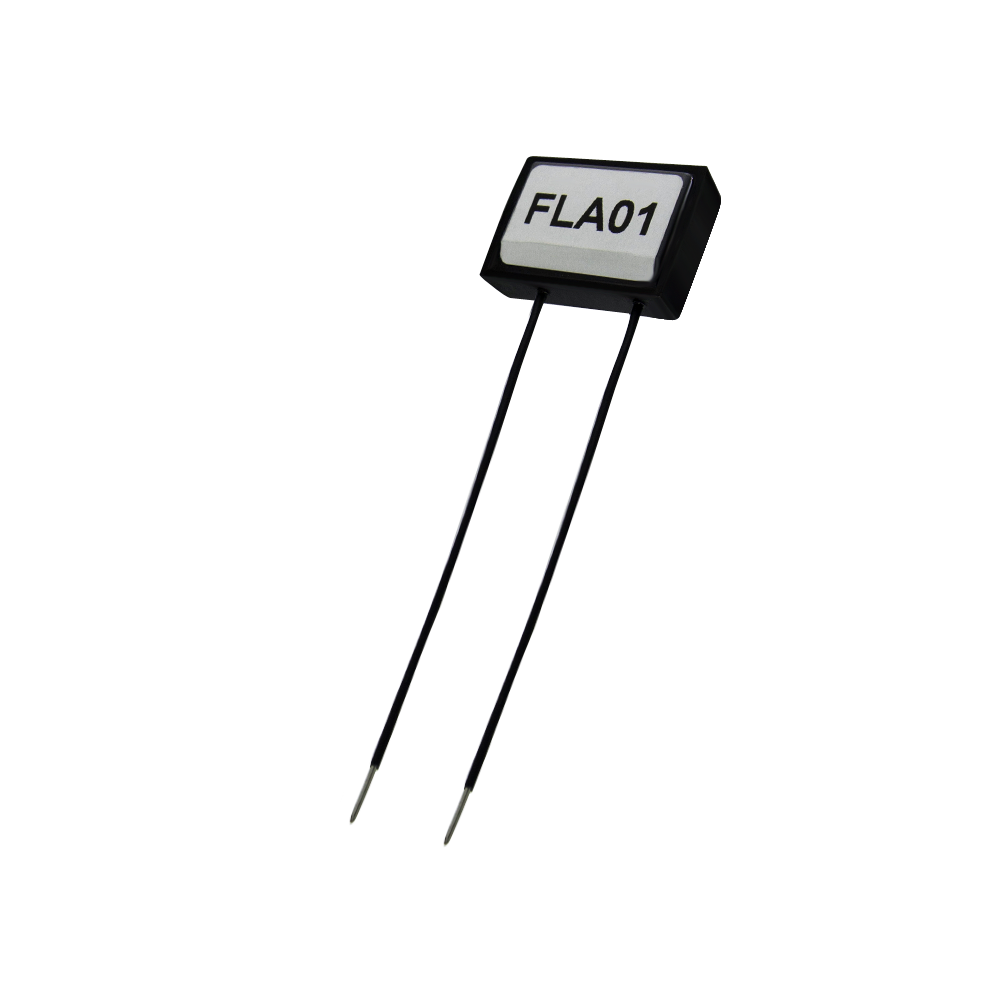
Used in fluorescent light fittings where dimmer/timer control is needed and is sold as an optional extra, a capacitor/resistor assembly used in the dimmer/timer control was made obsolete by the original manufacturer, leaving the customer struggling to find a replacement. The customer was desperate to find a solution, and so they approached Charcroft to ask if we could make a replacement.
Charcroft developed a design involving a KEMET capacitor and two values of resistors made by TT Electronics (Welwyn). These were soldered together both series and parallel and encapsulated into a plastic case. Charcroft worked alongside the customer to develop a product that met their precise requirements, allowing production of the lighting control-unit to continue; we now have a regular annual order for these parts.
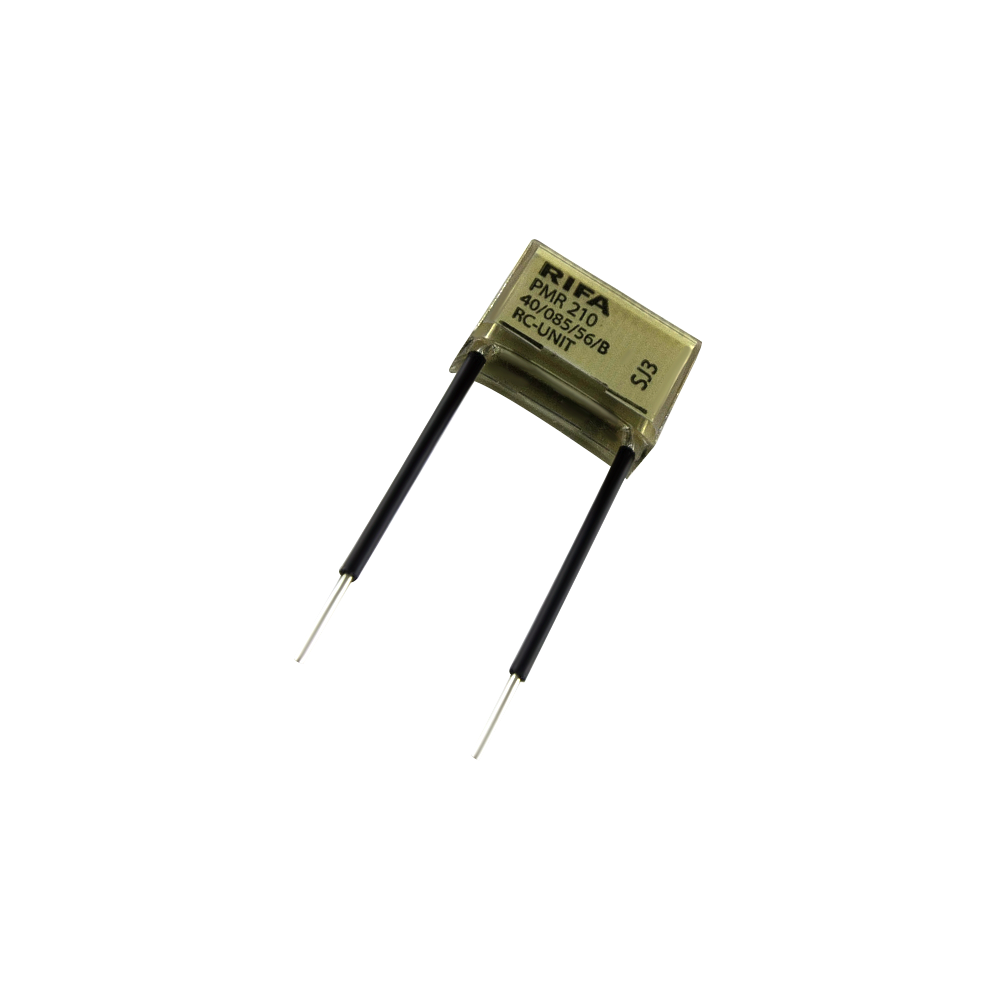
A customer had a requirement to fit insulated sleeves onto ‘snubber’ capacitors. Snubbers are used in switching circuits to reduce the voltage spikes created in switching circuits, which could result in over-voltage conditions, including arcing on the switch contacts – reducing life expectancy. In application, the capacitor leads were exposed and technicians carrying routine maintenance ran the risk of receiving electric shocks if the leads were accidentally touched. Charcroft developed a solution to this problem, which involved fitting heat-shrink sleeving along 80% of the length of the capacitor leads. The customer was unable to find a manufacturer capable or willing to execute the work for them, and so they then asked Charcroft to implement the manufacture of the solution for them. This involved developing and producing an automated process to handle large quantities of parts – we are now able to process 400 pieces per batch and we receive large regular requirements for these parts.
Our Product Specialist made a routine visit to a material-handling customer, where the customer mentioned that they had a requirement for a power supply to charge electronic equipment on forklift trucks for the local market. Our Product Specialist was able to advise the customer that we may be able to offer a solution. The customer then provided us with designs for two types of power supply, a 5v output device with micro USB connectivity and a 12v output version, based on the MTM PMD50 power supply. A third design covered an installation-pack to allow post-build fitment of the power supplies onto forklifts of various electrical architectures.
The designs were converted into CAD drawings by Charcroft and, following approval, samples of each design were built and submitted to the customer for testing and final approval. This allowed the customer to develop a bespoke solution suitable for the local markets or specific customers and has converted into production orders for all three lines with ongoing additional projects covering HMI systems & low-temperature operation of electronic systems..
An automotive customer who manufactures HVAC systems for off-road vehicles had been purchasing pressure switches, resistors and thermal sensors from us, and on a support visit from a Product Specialist, it emerged that they were also looking for a cable harness supplier. After the success of the Power Conversion project we undertook, despite automotive harnesses being more complex, both our Product Specialist and Engineering Team Lead were confident that we could meet the customers requirements. The prototype build is currently under development, and we are working closely with the customer to ensure we are meeting their exact specifications and finding solutions to any challenges that arise. The prototype stage is essentially setting out the fit and function, methods and pre-production builds for the customer, and we will be delivering the first samples shortly.