
How important is specialist distribution when managing obsolescence?
As challenging market conditions continue with no immediate signs of demand slowing down, sourcing components remains a struggle. The ongoing pressures of demand on manufacturers has led to a slew of components being made obsolete over the past months. With capacity at a premium, manufacturers are prioritising the production and supply of higher margin products, often at the expense of more mature, lower demand parts. Indeed, ongoing issues with demand into 2019 will likely see a continuation in component obsolescence.
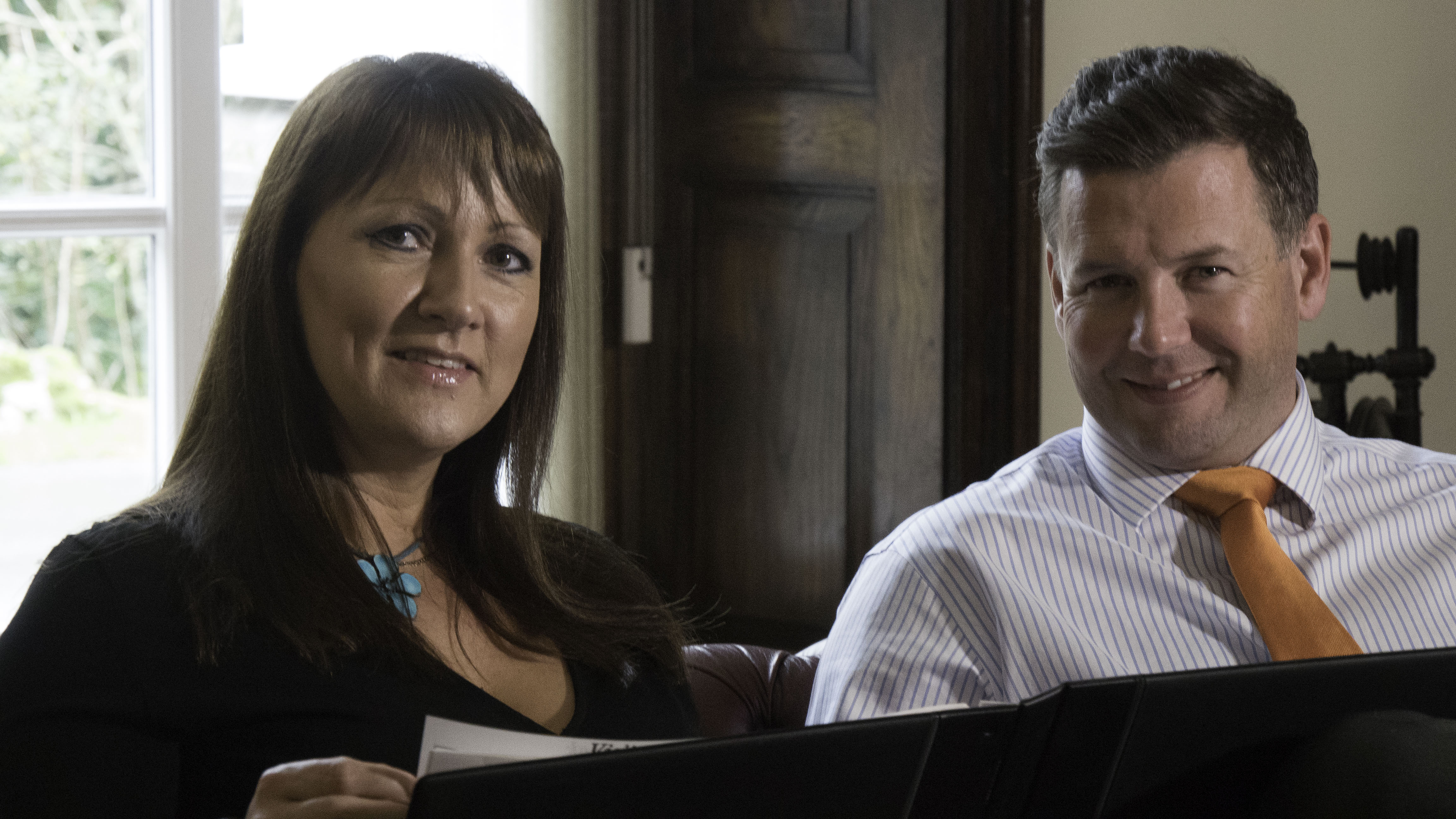
Large blue-chip companies often have no commitment to long term programmes, and so decisions on obsolescence are predominantly financially driven with little thought given to the potential impact. The long-reaching implications of these decisions may mean that we will see OEM’s struggle to source components for next stages of programme lifecycles over the coming months and years, with the more immediate market demands being prioritised over long term requirements.
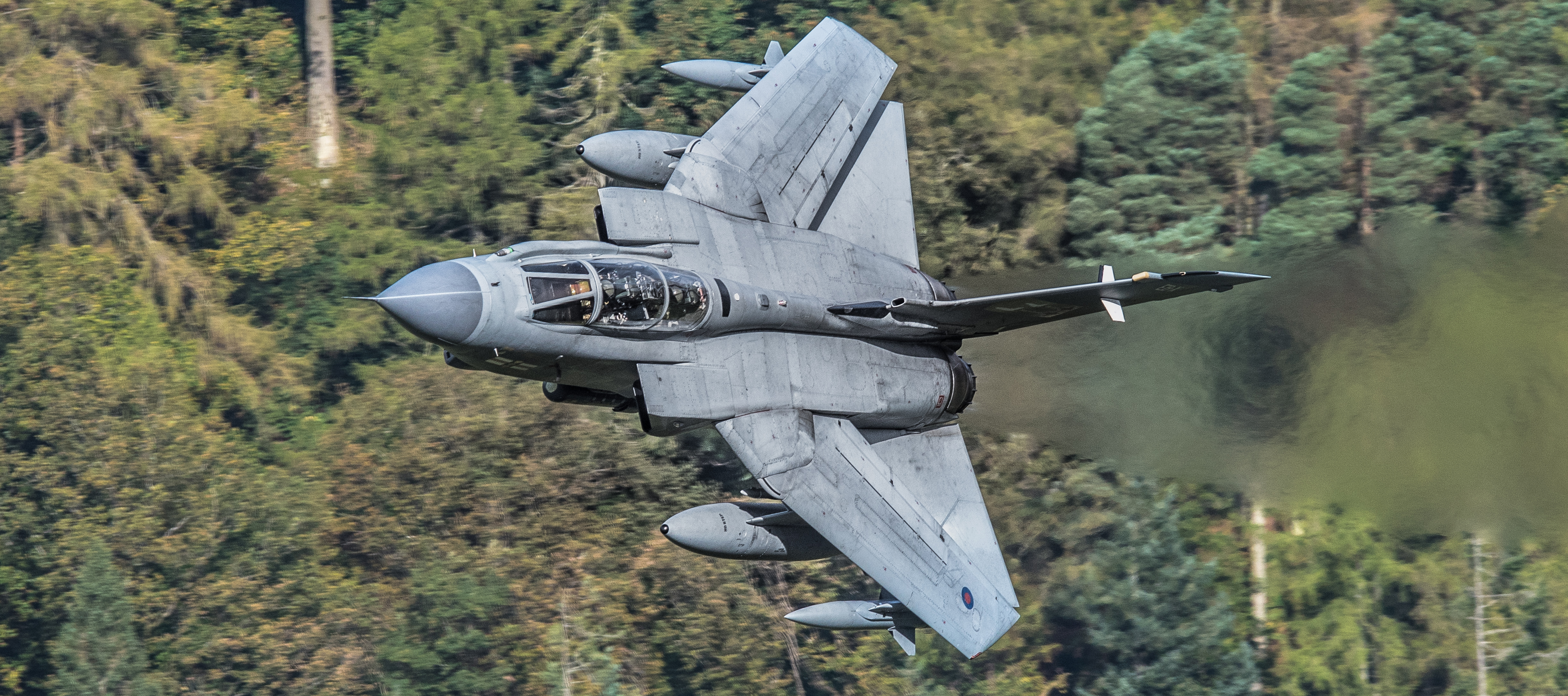
Particularly within the mil-aero market, the programme lifecycle is changing. We are now seeing more emphasis on refurbishment rather than new development, and so programme lifecycles are stretched out further than originally intended. The result of this is that component lifetimes are often required for longer than originally planned from a programme perspective, but this is not aligned with the manufacturers commitment to the provision of the component.
Specialist distributors, such as Charcroft, can assist with obsolescence management in ways that larger distributors often cannot. In instances where a component is made obsolete before the end of the programme lifecycle, we can support by sourcing alternatives, often by utilising access to legacy catalogues and datasheets to find the closest fit, form and function. If there is no alternative to be found, there is also the opportunity for us – as we have the capability, to manufacture a direct alternative, potentially using modern techniques and components of a higher specification, thus supporting the programme from cradle to grave.
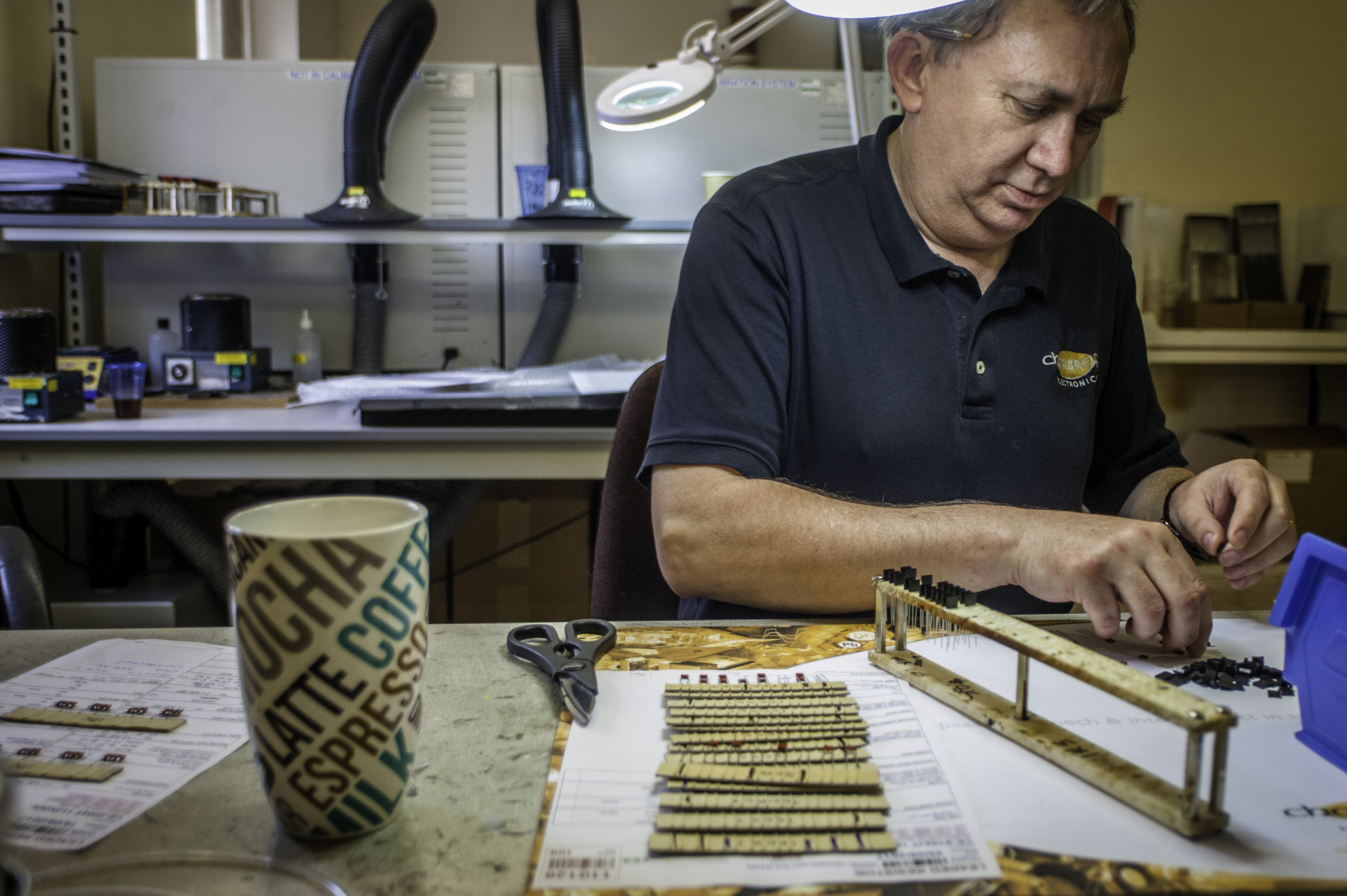
Sourcing of alternatives is but one facet of managing obsolescence. Industry knowledge and expertise is another efficient tool for mitigating the effects. When one manufacturer announced the first round of obsolescence for its tantalum buttons, Charcroft were able to foresee the potential implication of this in the long term, predicting the obsolescence of the whole range at a later date and advising customers to place orders to negate the impact as much as possible. This prediction has indeed come true with the full obsoleting of the range in 2019. With this initial foresight, customers had the potential to avoid the frantic rush on LTB and instead act to design-in alternatives.
Through-life specialist support for extended programme life cycles is something best handled by the experts. As the more ‘niche’ requirements of customers are falling to the wayside for the higher ticket items to be prioritised, Charcroft can help to bridge the gap between demand and availability. Efficient management of LTB opportunities and proactive management and forward planning of stock can also assist with ensuring support for obsolescence issues.